EQUIPMENT
- Home
- EQUIPMENT
Factory Scale and Precision Equipment
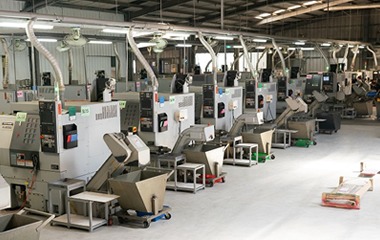
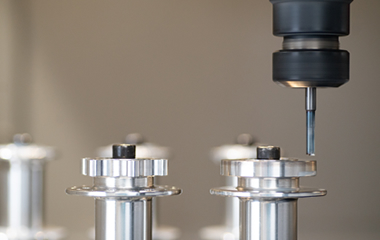

We operate a manufacturing facility spanning approximately 6,800 square meters (75,000 square feet), equipped with state-of-the-art multi-axis Mori-Seiki and Brother precision machines at the core of our production process. This enables us to simultaneously enhance production capacity and efficiency. Our facility is equipped with advanced capabilities for development, testing, quality control, surface treatment, machining, assembly, and packaging, ensuring that our products maintain a leading position in the bicycle components industry.
Warehouse Management System
We have implemented a modern warehouse management system to ensure efficient and precise inventory control.
With automated functionality, we can track inventory status in real time, optimizing the storage and distribution of all materials and products.
Precision Metal Processing | Highly Efficient & Stable Manufacturing Capabilities
We have over 150 high-precision metal processing machines, specializing in precision machining of metal components. Our strict quality standards ensure that our products meet various high-precision requirements.- Highly Stable Production: Ensures precise and consistent part dimensions, improving assembly efficiency.
- Flexible Production Scheduling: Quickly adapts to different batch sizes and customization needs.
- High-Efficiency Processing: Reduces processing time and enhances production efficiency.
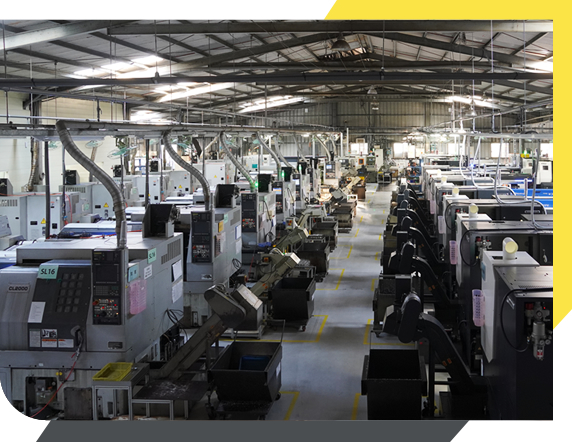
Anodizing Production Line | High-Efficiency Production, Stable Quality
We operate a fully integrated anodizing production line, providing one-stop service from manufacturing to surface treatment. This significantly shortens processing time, ensuring stable product quality and fast delivery.
- In-house Production: Reduces outsourcing wait time and accelerates delivery.
- Efficient Processing: Lowers production costs and enhances supply chain stability.
- Precise Quality Control: Ensures consistent product appearance and texture.
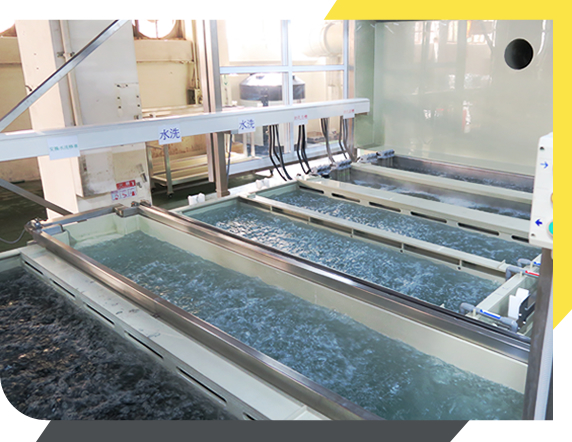
Aluminum Recycling & Reuse | Efficient Recovery, Less Waste
During precision machining, we are committed to aluminum recycling and reuse, reducing material waste while enhancing environmental sustainability in production.- Efficient Sorting & Recycling: Aluminum chips are sorted immediately after cutting to ensure high-quality recovery.
- Circular Reuse: Recycled aluminum can be remelted, reducing raw material consumption.
- Sustainable Production: Minimizes waste and reduces environmental impact.
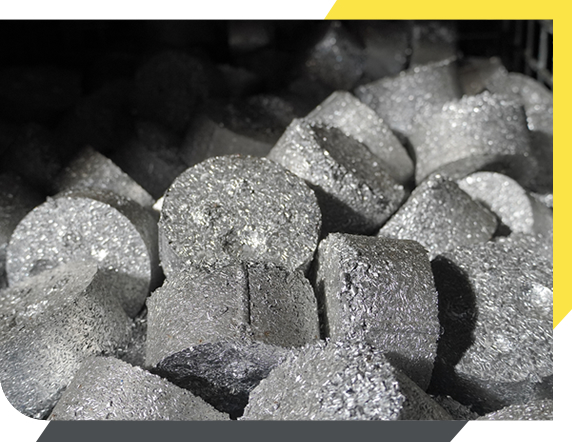
Cutting Fluid Circulation System | Enhance Machining Efficiency, Reduce Environmental Impact
Our comprehensive cutting fluid circulation system ensures smooth machining processes while minimizing resource waste and environmental pollution. Through automatic filtration and reuse mechanisms, production efficiency is significantly improved, and waste liquid discharge is reduced.
- Automatic Filtration & Reuse: Effectively removes impurities, extending the cutting fluid's lifespan.
- Stable Machining Quality: Maintains cooling and lubrication effects, reducing tool wear.
- Reduced Waste Liquid Discharge: Lowers the frequency of fluid replacement, reducing environmental pollution.
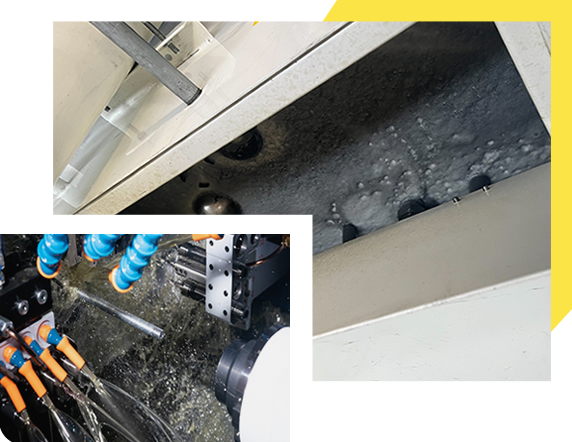
Awarded 2024 Green Enterprise
Saving energy and reducing environmental pollution throughout the entire process—from research and development, design, and manufacturing to recycling—helps conserve energy, minimize pollution, and promote resource recycling and reuse.
- 481 solar panels
- Recycled aluminum chips repurposed into aluminum grilles
- Reuse of wastewater from RO pure water machines
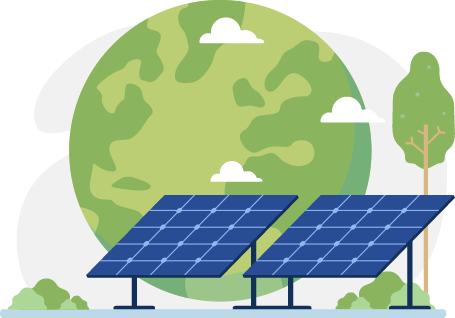